Using plywood has its advantages. Not only is it cheaper than other wood types, but it’s also resistant to warping and swelling. Warping is one of the most common problems with plywood, but laminating can eliminate this problem. But how can you laminate plywood? Read on to find out. This article covers the cost and applications of plywood laminates. Also read: What’s the advantage of laminating plywood?
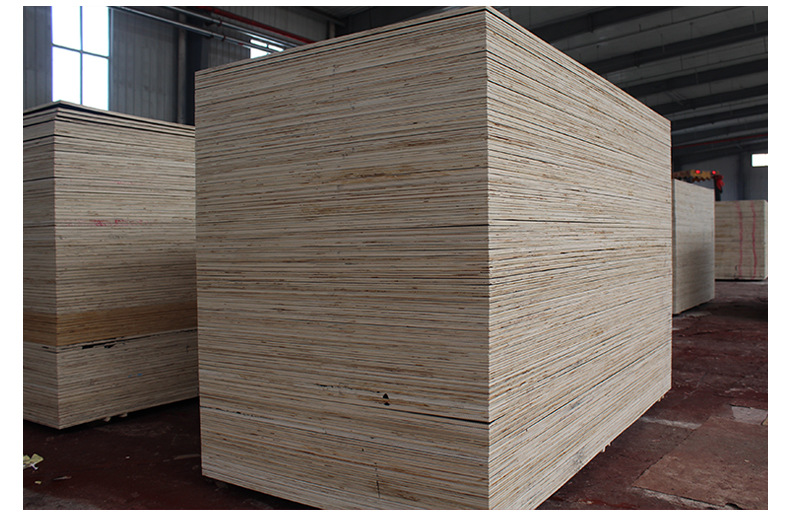
Precautions for laminating plywood
If you’re thinking of creating a project using plywood, you may be wondering how to safely laminate it. Luckily, there are a few precautions that you should take before you begin. Whether you’re constructing a furniture box or an elaborate wall-to-wall installation, you’ll want to consider some of the following safety precautions before you begin your laminating project.
Cost of laminating plywood
The process of laminating plywood begins with cutting the sheets and laying them out. This process is done in a machine and requires a significant amount of pressure. In order to secure hardwoods in the plywood, 200 psi of pressure is required, and this amount must be applied evenly across the entire surface. This is not the case for a 48×96 sheet of plywood, as you do not need this much strength. The press used in this process will be capable of providing 58 tons of pressure evenly across the entire surface.
The process of laminating plywood requires adhesives and hard pressing machines. Lamination improves the aesthetics of plywood by adding decorative laminate sheets. These sheets are placed on top of the plywood and form elegant decorative and protective surfaces. Veneers are slices of wood used in lamination. These are obtained from timber logs and manufactured by rotary cutting. Each individual wood layer is known as a ply. Laminated plywood is typically more expensive than traditional wood.
Resistant to moisture and swelling
The properties of laminated plywood are largely dependent on its bonding method. A PUR-based plywood with an alcohol-soluble resin is evaluated for physical changes under prolonged exposure to water. The tests are conducted under controlled laboratory conditions and measure the mass and thickness of the plywood specimen after one day of immersion in water. After five days of exposure to water, the test is repeated and the results are recorded. In addition to these test results, PUR-based plywood is also treated to improve resistance to fire, moisture, and biological attack.
The best way to ensure that your plywood is completely water-resistant is to install it in a well-ventilated, dry location. This will keep moisture from soaking into the wood and causing the material to become warped. This method will prevent the warping of the laminated plywood and protect it from moisture damage. For best results, check the plywood for cracks before installation. If any of them appear, they are caused by delamination.
Wood warping occurs due to its moisture content and relative humidity. High moisture content causes wood to shrink, while low moisture content causes wood to swell. The moisture content of wood is influenced by ambient air temperature, but this doesn’t significantly affect the equilibrium moisture content. Moreover, plywood is dimensionally stable compared to other wood-based building products. If the moisture content in wood is higher than the equilibrium moisture level, then it is likely to warp or expand.
Another factor that makes laminated plywood water-resistant is the veneer thickness. This varies depending on the thickness of the veneer. A typical plywood thickness has 50 percent veneers running in each direction and is assembled in a balanced way around the central plane. The more plies the panel has, the more stable it is. When assembling a panel, you should provide a minimum of 1/8 inch of space at the edges and ends. If you exceed this spacing, the panel could buckle.
A composite material with compressible faces could be used for furniture. Because it is highly water and alcohol resistant, it can be sanded and buffed. It is also highly valuable for interior paneling. Its water resistance is also important for acoustic panels and soundproofing. You may not have considered it, but it could be a viable option for you. If you’re in the market for a new product, look for a quality laminated plywood.
Applications of laminating plywood
Plywood can be classified according to its uses, such as structural, decorative, or marine. In the European Union, plywood is classified according to EN 636 (CEN, 2015) and Eurocode 5 (CEN, 1995) and by its hazard class for the environment. Depending on its use, laminated plywood can also be treated for improved chemical, fire, and biological resistance. This article will review some of the more common applications of laminating plywood.
Laminates come in various designs, colors, and textures. Their thickness varies from 0.8mm to 30mm. Many applications for laminated plywood include decorative tops and bottom surfaces. Manufacturers use hot-press techniques to produce pre-laminated plywood. These techniques are durable and resistant to heat and humidity. In addition to providing a high-end aesthetic appearance, laminated plywood is also fire and scratch-resistant, and has antibacterial properties.
Laminating plywood is a relatively simple process. The process involves the adhesion of two or more sheets of wood, usually a veneer on top of a layer of wood. These layers are then bonded together with heat and pressure to create a strong bond between the sheets. In general, the number of layers depends on the use of the plywood. Plywood is used in architectural applications for roof sheathing, siding, floor underlayment, and structural diaphragms.
Plywood has many different applications. For instance, in building construction, plywood sheets are 4 ft by 8 ft. However, larger sheets may be required for certain applications such as boat building. Generally, the plywood trees are smaller than those that grow lumber. Plywood companies own and manage these forests carefully. For this reason, they are more likely to produce high-quality plywood. And this makes the process of plywood manufacturing a multi-billion-dollar industry.
Decorative and protective laminate are two of the common uses of laminated plywood. Formply, for instance, is an Australian structural standard that meets the requirements for building bridges and concrete formwork. And the price is also very affordable. And while the prices of plywood are expected to remain relatively stable until 2022, the benefits of these products will continue to be significant. When it comes to applications, laminated plywood can be used for anything from window frames to false ceilings to partitions and racks.