The process of processing logs to produce commercial plywood:
logs → logs sawing → wood section steaming → wood section peeling→ veneer spinning → veneer drying → veneer finishing → gluing → pre-pressing → hot pressing → edge cutting → sanding → inspection and grading → packaging into storage.
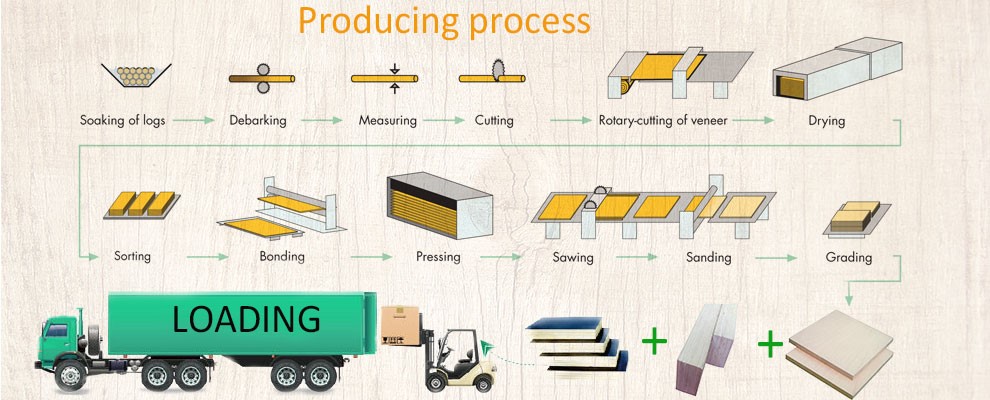
The process flow of veneer processing to produce decorative plywood:
veneer finishing → gluing grouping → pre-pressing → hot pressing → cutting into → sanding → inspection and classification → packaging into storage.
Process flow production of plywood
The process flow of plywood manufacturing focuses on identifying waste and reducing it. The balance of flow along the layup line lends itself to the terminology of lean production. In the production of plywood, the finished inventories and yields may be held to wait out low market prices, while the remaining panels will be sold. This process leads to an overall lower cost producer. During the production process, all steps are continuously monitored for quality control.
After sorting the sheets, the edges are varnished. The sheets are then stacked to be transferred and dried. During the production of plywood, the thickness of each veneer is measured, so that the product’s strength is consistent across different veneer layers. The finished plywood sheets will vary in width and length. The process flow of plywood manufacturing is illustrated below. Listed below are the steps in the production process. If you are interested in learning more about plywood production, check out the following links:
First, the logs are processed. After this, they are split into several layers. The pieces are then glued together with a water-proof glue. The veneers are then laid in sandwiches to form plywood. Then, the layers are sanded to smooth them out. This process ensures that the veneers will not warp or split. The process of manufacturing plywood is very similar to the manufacturing of any other type of wood product.
Pressing plywood. The plywood sheets are pressed together. The pressure is applied using hydraulic or pneumatic presses to achieve the desired thickness. The pressure hardens the glue quickly, and the combined veneer is ready for the next step. Hot pressing is a more complicated process, which involves combining all these processes into one semi-automatic line. Then the finished plywood is ready for its final destination. It is also the process that gives it its unique and durable appearance.
Log selection
A good plywood manufacturer is committed to maintaining the highest quality standards. Log selection is one of the most critical aspects of a plywood manufacturing process. Logs are harvested at various stages of production. A process that begins with the log yard stocking and progresses to the pressing and gluing stages is known as the process flow. The sheets are then scanned for thickness before they are transferred to a stack for drying and transfer.
Log selection is the first step in the production of a quality plywood. A plywood manufacturer must choose logs with good physical properties and a sustainable forest concession. In order to process thin layers, the logs are submerged in water for a period of time. Some plywood mills use heat to enhance peeling. Hydrothermal processing improves the quality of the veneer produced. When the logs are processed, they are stacked horizontally before being cut into pieces.
Once the logs are sorted, they are marked for felling. Depending on their size, the logs are either cut with gasoline-powered chain saws or large hydraulic shears mounted on feller vehicles. The logs are then debarked by sharp-toothed grinding wheels. The debarked logs are carried to the mill by chain conveyor. The saw cuts the logs into lengths appropriate for standard eight-foot sheets.
Veneer rotary cutting
plywood production is the most widely used in the production of rotary cutting method of veneer, the thickness of the face and back plate generally about 0.6mm, core board, long board thickness is generally about 1.8mm. The process loss is the largest thinnest plywood, one is due to the wood segment is not round, a considerable part of the broken veneer can not be used; second is the rotary cutting machine chuck on the two ends of the wood segment of the clip and end loss; third is the loss of wood core. Veneer rotary cutting waste generated for the broken veneer and wood core, it can be seen that the amount of veneer rotary cutting loss with the material, diameter and equipment performance, this part of the loss rate of 15% to 25%,lowes plywood prices.
Veneer drying
the moisture content of the veneer after rotary cutting is very high, the veneer must be dried to meet the requirements of the gluing process requirements. After drying, the size of the wood becomes smaller, called dry shrinkage. The length, width and thickness of the veneer will shrink due to the reduced moisture content. The shrinkage loss is related to the species of the veneer, the moisture content of the veneer and the thickness of the veneer. The dry shrinkage loss rate is generally 4% to 10%.
Veneer finishing
Veneer finishing includes shearing, splicing and repair. The dried strip veneer, zero piece veneer is cut into specification veneer and spliceable veneer, narrow veneer is spliced into whole veneer,4×4 plywood defective whole veneer can be repaired to achieve the quality requirements of the process. The amount of waste veneer generated by this process is related to the log material, the quality of the rotary cut veneer, the quality of the dried veneer and the familiarity of the operator with the veneer standards, etc. The plywood supplier loss rate is generally 4% to 16%. The loss rate of the process of directly imported veneer processed into birch plywood lowes is generally 2% to 11%.
Hot pressing
The 8mm plywood glued panels are firmly glued together by a certain temperature and pressure. Hot pressing with the change of temperature and moisture content of the slab, the wood is gradually compressed and the thickness of the slab is gradually reduced. The loss is compression loss, and the cdx plywood home depot hot pressing temperature, unit pressure, hot pressing time, species and moisture content and other factors related to the loss rate is generally 3% ~ 8%.
Cutting edge
The 4×8 plywood home depot hot pressed rough board is cut into specification boards. The amount of edge waste cut off is related to the processing allowance of plywood, the size of the width, the larger the width of the plywood, the smaller the loss rate of cutting edge, generally 6% to 9%.
Sanding
The surface of marine plywood lowes is sanded to make the board surface smooth and beautiful. The waste produced by this process is sanding when the quality of veneer is good, the sanding quantity is small and the loss rate of sanding is generally 2% to 6%.
In the case of normal material, the loss rate of raw wood processing and plywood production is generally 47% to 55%, and the loss rate of directly imported semi-finished veneer processing and plywood production is generally 16% to 26%.