Based on the analysis of the development status of particleboard industry, this paper studies the impact of manufacturing process factors on the water absorption expansion rate of particleboard through experimental data analysis. It is summarized that the following manufacturing process factors affect the expansion rate of particleboard, including hot pressing time, hot pressing temperature, hot pressing pressure, density of the board, moisture content of the shavings, amount of glue, etc. The experimental results show that reducing the water absorption thickness expansion rate of particleboard is mainly obtained by reducing its irreversible thickness expansion rate. At the same time, it is also necessary to choose a reasonable plate size and reduce viscoelastic deformation and glue joint damage.
With the continuous development of manufacturing technology, the production technology level of building decoration materials has been continuously improved, the process methods in building materials production have been continuously improved, and the processing efficiency of many raw materials has been improved. Particle board is our common building material. Due to the influence of the manufacturing process during the production and manufacturing process, its thickness expands during the water absorption process, which leads to a decrease in the quality of the building material. Therefore, in order to ensure the quality of building materials, identify problems in the production process of particleboard, and improve its expansion rate after water absorption, certain experiments will be conducted below to draw conclusions and provide some reference for the majority of particleboard manufacturers.
Ⅰ.Overview of particle board
Particleboard a kind of artificial board which is made by cutting wood processing residues, small diameter wood, sawdust etc, into fragments of a certain size or shaving materials made from non-timber plants, drying them, mixing them with glue, waterproofing agents etc, and pressing them under a certain temperature and pressure. The use of the above raw materials can comprehensively utilize processing residues and at the same time protect the sustainable development of the ecological environment. Particleboard is mainly used in interior decoration, furniture manufacturing, decorative veneer production, structural construction panels and carriage, ships, packaging boxes, container panel manufacturing and other fields.
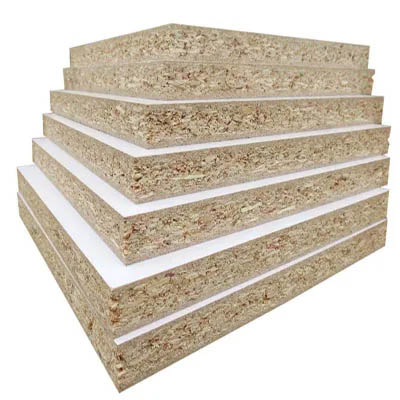
Ⅱ.Development status of my country’s particle board industry
2.1 Industry development status
China’s particleboard production has experienced a repeated process from rising in the 1980s to declining in the 1990s, and then rising again in 2000. After the particleboard products were abandoned by the market due to poor quality and other reasons, many particleboard companies learned their lessons, introduced advanced foreign production lines, and improved their own process levels. Therefore, the quality of Chinese particleboards has improved significantly in recent years, and the demand has increased year by year.
According to incomplete statistics, my country’s total particleboard production has exceeded 10 million cubic meters. At present, my country’s particleboard industry has only a dozen of the world’s most advanced German fully-automatic continuous flat-pressing production lines, which are mainly concentrated in a few companies such as Zhongyan Yingang, Jiangsu Daya, Jilin Forest Industry, and Fujian Furen, large-scale artificial board enterprises.
2.2 New particle board products
After decades of development, the particleboard industry has become increasingly mature in terms of production technology and product market. In recent years, in addition to ordinary particleboards, some new products such as flame-retardant particleboards and cement particleboards have been launched, maximizing the needs of different fields and consumer groups.
2.2.1 Flame retardant particle board
Flame-retardant particleboard is a particleboard that has been treated with flame-retardant technology to make it flame-retardant. “Flame retardant” does not mean “non-flammable”. Any substance will burn under certain temperature conditions. Compared with ordinary particleboard, its essence is to delay and inhibit the spread of combustion and reduce the probability of ignition. It is a technology that fundamentally inhibits and eliminates uncontrolled combustion. The main features of flame-retardant particleboard are: inhibiting and delaying combustion, and reducing the probability of ignition.
2.2.2 Cement particle board
Cement particleboard is a new type of building that uses cement as the cementing material, wood particle fibers as reinforcing materials, and an appropriate amount of chemical additives and water to complete the consolidation of cement and wood materials under pressure. Material.
The characteristics of cement particle board are: dense structure, smooth surface, green and environmentally friendly, pollution-free, high strength, anti-static, fire-proof, waterproof, sound insulation, moth-proof, and anti-corrosion. It can be sawed, drilled, glued, nailed and finished.
Ⅲ. Experimental materials and methods
3.1 Experimental materials
In the following experiments, we choose wood with better quality as the production material of particleboard. These include big blue poplar, Xing’an larch, Korean pine and our common white birch trees that grow in northeastern my country. Since these trees have grown in the northeastern region of my country for many years, their material density is relatively high, making them suitable for the production of particle boards. The adhesives used to produce particleboards are YQJ.A isocyanate adhesive, DN.6 urea-formaldehyde resin adhesive and DP-A phenolic resin adhesive. However, in actual particleboard production we need to carry out a certain proportion of the above three finished gelling agents. The proportions form a homemade adhesive material.
3.2 Experimental methods
The particleboard produced in the experiment must be formulated in accordance with the requirements of the board specifications formulated by the corresponding country. These include the format size of the board, the nominal thickness of the board etc. The three-stage pressurization method used in plate production is used to pressurize the plate. In addition, instruments must be used to measure various technical elements of the board, including the static bending strength, density, moisture content, water absorption expansion rate and irreversible thickness expansion rate of the board.
Ⅳ.Result discussion
4.1 Hot pressing temperature
In the manufacturing process of particleboard, it is necessary to ensure the format and hardness of the board, so the board must be hot-pressed and heated to fully integrate the gelling agent in the board into the particles. The value of the temperature determined in this process becomes an influencing factor in controlling the quality of the plate, that is, the hot pressing temperature. In order to ensure that the particleboard produced can bond better during bonding, ensure the curing of the adhesive, and eliminate moisture, we need to hot-press the particleboard. The components of wood include cellulose, hemicellulose and lignin. In the process of physical state changes, they are mainly related to the existence form of water. When the temperature of hot pressing is controlled at a certain value, the moisture in the particleboard will undergo certain physical changes. Usually we use the glass transition temperature to measure. For the hot pressing temperature of particleboard, a certain temperature increase must be carried out while pressurizing. This causes the wood to undergo rheology in a shorter period of time. This results in large viscoelastic deformation and viscous deformation. These deformations will increase as the temperature increases. Therefore, when producing particleboard into boards, we need to increase the hot pressing temperature appropriately to meet the requirements for adhesive curing of the particleboard under hot pressing. This also reduces the water expansion rate.
4.2 Hot pressing time
The main components of particle board are wood from different tree species. During the hot pressing process, a certain amount of viscoelastic deformation will occur inside the board, and at the same time, the molecular chain segments inside the material will also slip to a certain extent. As the pressurization time is different, the degree of slip produced is different. Generally speaking, the longer the hot pressing time of particleboard, the greater its irreversible expansion rate will be. But this expansion rate does not increase endlessly. When the hot pressing time increases to a certain level, it will show a decreasing trend. Many researchers believe that this is because long-term hot pressing causes the viscoelastic deformation of the plate to be converted into viscous deformation, or the enhanced effect of moisture produces complex changes in physical properties, which affects the irreversible expansion rate of the plate.
4.3 Hot pressing pressure and board density
During the processing of particleboard, the amount of hot pressing pressure determines the density of the board, and the density of the board also determines the overall quality of the board. Generally speaking, when the density of the board is high, when the particle board is hot-pressed, the initial compression deformation will be larger. This is because the internal voids of the board are compressed, causing a certain displacement of the structure and even cell pressure. collapse phenomenon. As a result, some of the load effects inside the plate disappear. Usually we use a thickness gauge to measure the thickness of the board. To ensure that its thickness meets the actual production technical parameter requirements. In addition, if the density of the board is too high, the compression space is small, and the moisture entering the inside of the board is restricted, which in turn makes it difficult for the moisture inside the board to diffuse. Therefore, we can conclude that the greater the density of the board, the greater the deformation will eventually occur and the irreversible thickness expansion rate of the particleboard will be too large. On the contrary, when the internal density of the board is smaller, the space available for compression inside the board will be reduced, and the compression rate of the board will be reduced. The heat transfer energy efficiency inside the board will decrease, which will eventually affect the curing of the adhesive on the board and affect the adhesive effect. Therefore, we can say that to ensure the quality of particle board, we must first ensure that its density meets the requirements. The higher the density, the stronger the physical stability of the board.
4.4 Moisture content of wood shavings
The main material of particle board is wood chips. Because it is made of wood, it can absorb a certain amount of moisture appropriately. When the moisture in the wood particles exists, the particle board is subjected to heat pressure, and the physical properties of the board are appropriately reduced. The glass transition temperature of some constituent substances. Researchers have reached the conclusion through certain research experiments that when the plate material used in the experiment is absolutely dry, when the hot pressing temperature increases, the elastic compliance and delayed elastic compliance of the plate will increase slightly. If the board used in the experiment contains a certain amount of moisture inside, then when the temperature increases, the elastic compliance and delayed elastic compliance will increase. Therefore, we can conclude that the moisture content of wood shavings has a certain impact on the production of boards.
4.5 Glue amount
Under the premise that other conditions are certain, the amount of glue applied on the particle board determines the number of glue joints in the board. Increasing the amount of glue applied will increase the number of glue joints, allowing the system to withstand greater internal stress without causing damage to too many glue joints, thus reducing the irreversible thickness expansion rate caused by damage to the glue joints and improving other properties. However, the increase in the amount of glue will increase the cost of the particleboard accordingly. Therefore, for general-purpose particleboards, it is not advisable to increase the amount of glue to improve the dimensional stability.
All in all, particle board is a common building decoration material, and its processing and manufacturing level has also been greatly improved. In the article, the requirements for reducing the water absorption thickness expansion rate of particleboard or improving the dimensional stability of the board have been solved, mainly by increasing the irreversible thickness expansion rate of the board. In order to achieve this result, we must consider various factors involved in board processing, including the hot pressing time and hot pressing temperature of the board, the density of the board, the moisture content of the wood shavings, the type of adhesive, the amount of glue applied etc. By comprehensively considering the above factors, we can produce particleboards that are more in line with actual needs, and can greatly improve the quality of particleboard boards.