Medium density fiberboard can replace plywood and hard fiberboard products. It can be used not only in the decoration industry, but also in the automotive industry. It has high economic benefits and good market prospects. In the next few years, medium-density fiber decorative materials with waterproof, fire-resistant and environmentally friendly properties can have huge development space and significant advantages.
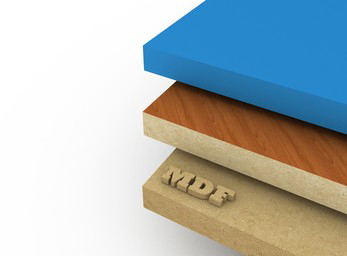
Medium-density fiberboard is one of the three traditional types of man-made boards. China is the main producer and consumer of medium-density fiberboard. East China, South China and Central China are the three major fiberboard production areas in China. Fiberboard production enterprises are mainly concentrated in Shandong, Guangxi, Jiangsu, Guangdong and Hebei provinces. At present, medium-density fiberboard is widely used in the production of furniture, interior decoration, cabinets and customized home furnishings. After years of development, the quality of medium-density fiberboard products has been greatly improved, but there are still certain problems.
1 Introduction to Medium Density Fiberboard
Medium Density Fiberboard (MDF) is a kind of man-made board made of wood fiber or other plant fiber as raw materials. After being prepared into fibers, urea-formaldehyde resin or other suitable adhesives are applied, and finally hot-pressed. Its density is 0.65~0.80g/cm3. Due to its dense texture, uniform structure, good mechanical properties and excellent board processing performance, medium density fiberboard has been widely used in furniture making, floor production, composite door production, interior decoration and decoration etc. It is one of the important interior decoration and decoration materials. The main implementation standard of medium density fiberboard products is the recommended national standard GB/T11718-2009 “Medium Density Fiberboard”.
2 Overview of the development of medium density fiberboard
China’s research and development of medium density fiberboard began in the mid-1970s. China’s first medium density fiberboard production line was built in the early 1980s. In the 1990s, China’s medium density fiberboard industry was in a period of rapid development. Although China’s medium-density fiberboard started late, it has developed rapidly, with annual output increasing from 5.14 million m3 in 2000 to 57.69 million m3 in 2015. It is one of the fastest-growing man-made board products in China. By the end of 2015, there were 667 fiberboard production lines in China, with an annual total production capacity of 50.88 million m3, a decrease of 0.6% from the previous year, showing a negative growth trend for the first time. From the perspective of the distribution of medium density fiberboard manufacturers in China, except for the Tibet Autonomous Region and Qinghai Province, there are medium density fiberboard manufacturers in all provinces and regions, but they are mainly concentrated in Shandong (capacity 7.5 million m3), Hebei (capacity 4.44 million m3), Sichuan (capacity 4.29 million m3), Guangdong (capacity 4.04 million m3), Anhui (3.59 million m3), Jiangsu (capacity 3.51 million m3), Henan (3.32 million m3), Hubei (3.12 million m3), Yunnan (1.88 million m3) and Guangxi (capacity 5.98 million m3). At present, there are about 400 medium density fiberboard manufacturers in China, of which large, medium and small enterprises account for 10%, 35% and 55% respectively. In the development of China’s medium density fiberboard, a prominent problem is that most manufacturers are small in scale and have backward equipment and technology, especially some enterprises do not meet the requirements of the National Development and Reform Commission’s “2011 Product Structure Adjustment Guidance Catalogue” that the annual design capacity of a single line of medium density fiberboard production is more than 50,000 m3. Shandong Province, which produces the most MDF in China, has 43 MDF production lines with an annual design capacity of less than 40,000 m3, accounting for 46.24% of the total. Due to raw materials and other reasons, the output of 10 provinces such as Shanxi, Sichuan and Jiangxi does not meet the equipment design capacity level. Looking at China’s existing forest resources, it is impossible to support the rapid development of the MDF industry. Therefore, in the transformation and upgrading of enterprises, small-scale MDF enterprises with backward equipment that do not comply with national industrial policies must be eliminated, and the concept of relying on quantity for efficiency must be reversed.
3 Market Analysis
Europe and the United States are the main export markets for China’s wooden furniture, laminate flooring and other products. In order to make the exported panel furniture, laminate flooring and other products meet the mandatory formaldehyde emission standards of the United States, many processing companies have to import high quality medium and high density fiberboards. In 2016, China’s medium density fiberboard imports totaled 263,800 m3, an increase of 10.64% over the same period last year, and an increase of 25,400 m3; in the first four months of 2017, China’s medium density fiberboard imports totaled 77,200 m3, a decrease of 2.23% over the same period last year. In recent years, the international market for medium density fiberboard and laminate flooring has been seriously affected. In 2016, China’s medium density fiberboard and laminate flooring exports totaled 2.972 million, a decrease of 8.75% over the previous year, and a decrease of 285,000 m3. Under the passive situation of low medium density fiberboard exports, after looking for export markets in all directions, good results have been achieved. In the first four months of 2017, China’s medium density fiberboard and laminate flooring exports totaled 931,100 m3, an increase of 8.46% over the same period last year. With the establishment of green wall gold for composite wood products and furniture products in the world, as well as the high transparency of international environmental protection standards, coupled with the awakening and enhancement of domestic consumers’ environmental awareness, composite wood products and furniture below the E2 environmental protection standard will become increasingly difficult to sell. Therefore, the demand for domestic environmentally friendly boards may experience a “blowout”. According to the data of the “2016 National Supervision and Sampling Quality Announcement on Medium Density Fiberboard Product Quality” issued by the General Administration of Quality Supervision, Inspection and Quarantine, 160 batches of products from 160 medium density fiberboard manufacturers in 11 provinces in China were sampled, of which E2-grade boards accounted for 31.2% and E2-grade boards accounted for 68.8%. Some batches of products were seriously unqualified, and the formaldehyde emission detection value even exceeded the standard value by more than 3 times; some other manufacturers reduced the amount of glue in order to reduce the formaldehyde emission, resulting in insufficient bonding between fibers, resulting in unqualified physical and mechanical performance indicators of the board. Therefore, improving the environmental protection standards of medium density fiberboard is a difficulty that most manufacturers must overcome. If the environmentally friendly combination technology of diatomaceous earth flame retardant fiberboard can be promoted in China, it will undoubtedly lay the foundation for improving China’s national environmental protection standards for panels, furniture and home products.
4 Study on the environmental performance of medium density fiberboard
4.1 Modification of urea-formaldehyde resin
Usually, formaldehyde is excessive when urea glue is prepared, so the appropriate molar ratio of formaldehyde and urea is very important. The method of reducing the molar ratio of formaldehyde and urea can be adopted to modify the urea-formaldehyde resin. The appropriate F/U molar ratio is 1.2~1.4. Reducing the F/U molar ratio of urea glue will reduce the formaldehyde emission, but the negative effect is that the bonding strength of urea glue is significantly reduced, so other compensatory measures must be taken. In addition, the formaldehyde emission can be reduced by adding other glues (such as melamine, etc.) to the urea glue, and the dimensional stability and water resistance of the board can be improved, but this will increase its production cost; in addition, fillers such as polyvinyl alcohol and soybean starch can also be used to modify the urea-formaldehyde resin adhesive; new environmentally friendly flame retardant glue or formaldehyde-free new environmentally friendly adhesive can also be used. The current national standard has stipulated that the maximum free formaldehyde content of urea-formaldehyde glue for fiberboard is 0.3%, but the free formaldehyde content of urea-formaldehyde glue produced by Chinese companies currently mostly exceeds the standard.
4.2 Adjusting the hot pressing process
The hot pressing process has a decisive influence on the final performance of medium density fiberboard products. As the hot pressing temperature increases and the hot pressing time increases, the formaldehyde release decreases. However, the extension of hot pressing time and the increase of temperature will increase energy loss, reduce production efficiency, increase product costs, and even reduce the quality of medium density fiberboard products. Therefore, adjusting the hot pressing process does not have a very obvious effect on reducing free formaldehyde.
4.3 Adding formaldehyde scavenger
Urea glue is an acidic curing resin. It is best not to affect the curing speed of the glue by adding neutralizers or acidic formaldehyde scavengers. After curing, the substance that reacts with acid can make the glue layer nearly neutral. For example, adding 20% glass powder can achieve this goal. At present, there are many preparations that can absorb formaldehyde at home and abroad, such as the SL-N formaldehyde scavenger, the FS-1 free formaldehyde scavenger, uses sodium lignin acid as a formaldehyde scavenger to reduce formaldehyde content, Japan’s FC-5 formaldehyde scavenger, Belarus Lyubliner-IP uses wood processing residues to make adsorbents etc; acetyl ammonium, sodium bicarbonate or urea solution can also be used to impregnate or spray single boards. At present, these methods still have problems such as unstable effects and high costs, and have not been widely promoted and used.
As people’s awareness of safety, health and environmental protection continues to increase, as well as the requirements for environmental protection-related standards at home and abroad continue to increase, people not only have higher requirements for the physical and mechanical properties of medium density fiberboard, but also have higher environmental performance and functions. It is also used as an important indicator to judge its quality. In recent years, the demand for products has mainly been in the furniture industry, interior decoration and construction industry, and the production of medium density fiberboard with fireproof and environmentally friendly properties will have huge development space and significant advantages.