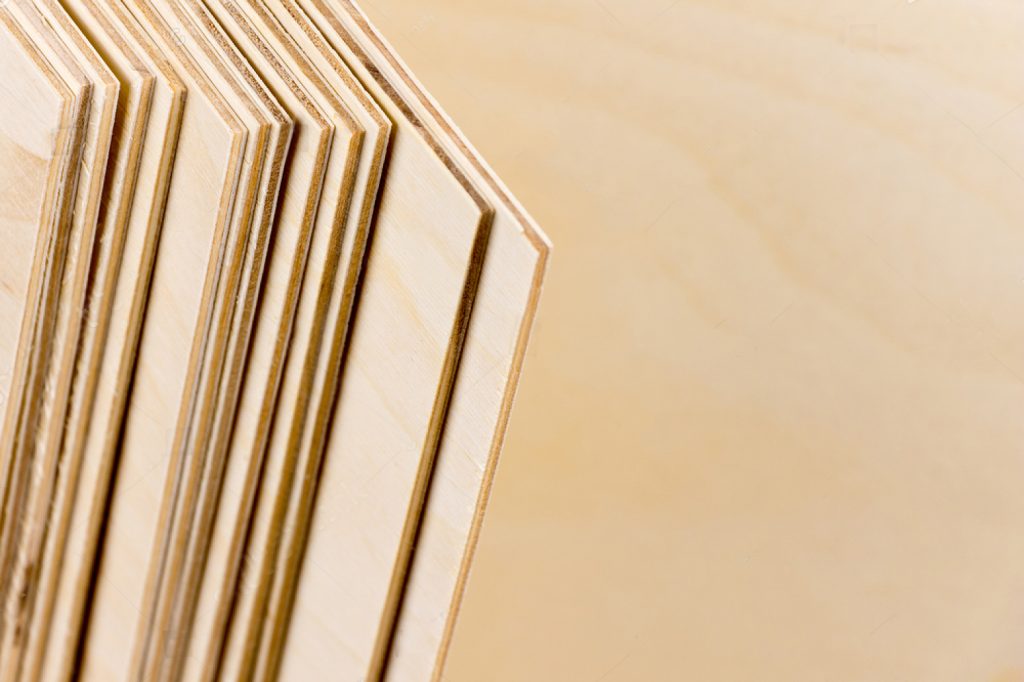
Compared with traditional steel formwork and wooden formwork, plywood formwork is popular as soon as it is put on the market because it has light weight, high strength, good toughness, can save a lot of steel and wood, has a high turnover rate, and is more economical. It is widely used in multi-story residential buildings, high-rise residential buildings, commercial buildings, bridges and other projects. Years of construction practice have proven that plywood formwork can greatly reduce workers’ labor intensity, is convenient for construction, easy to assemble and splice, and has low cost. Its use is increasing, but its construction quality depends to a large extent. Due to the technical level and quality awareness of workers, common problems such as mold runout, mold expansion, slurry leakage, uneven interfaces, and misaligned seams may easily occur if the mold assembly is not careful. How to effectively prevent and control the occurrence of the above common quality problems is the key to ensuring the quality of the main project.
1.Causes of common diseases
(1) Not paying enough attention to the formwork production and assembly plan, and not carefully preparing the assembly plan; or although a feasible assembly plan was prepared, during the actual construction, the formwork workers discounted it in order to save labor and time; or the selected assembly plan was It does not conform to the actual situation of the project.
(2) Failure to grasp the quality of plywood and its auxiliary materials when purchasing, or purchasing inferior materials to save costs, causing premature distortion, deformation and cracking during use.
(3) In order to save costs, the number of turnover times of formwork is blindly increased, resulting in serious damage to the formwork and the quality of concrete pouring cannot be guaranteed.
(4) There was no effective technical explanation before construction or the explanation was not in place. During the construction, quality inspection technicians lacked inspection or the inspection was just a formality, especially the lack of inspection of formwork splicing, supports and fasteners.
(5) During the lifting and installation process, workers carried out rough construction and failed to take effective anti-collision measures, resulting in deformation of the formwork and damage to the edges and corners.
(6) Failure to follow the dismantling plan or operating procedures during dismantling, and forced prying, resulting in man-made damage.
(7) There is no effective protection for reused templates.
(8) The supervisors did not carefully review the formwork assembly plan. The inspection of the formwork during the hidden acceptance was just a formality, and they ignored the inspection of the formwork strength, seams, elevation, support system, fasteners, etc.
2.Preventive measures
In order to reduce the occurrence of the above common quality problems and improve the quality of the project, in view of the causes and based on construction experience, the following measures were taken during the construction, which greatly improved the quality of the project, increased the number of template turnovers, and reduced the project cost;
(1) Before construction, you should carefully familiarize yourself with the construction drawings, combined with the actual project, and prepare and design a feasible formwork and bracket installation and removal plan based on the project structure form, load size, foundation soil type, construction equipment, and material supply and other conditions.
(2) Check the procurement of materials to ensure that the quality of plywood meets the on-site construction requirements.
(3) Replace damaged and deformed formwork in a timely manner and control the number of turnovers to ensure the quality of concrete forming.
(4) When installing the upper formwork and brackets of the cast-in-place structure, the lower floor slab should have the bearing capacity to withstand the load of the upper layer, or a bracket should be added; the columns of the upper and lower brackets should be aligned, and pads should be laid.
(5) Strengthen the protection of finished and semi-finished products, ensure neat and orderly classification and clear labeling, and store templates that will not be used in the short term neatly and do daily covering work to avoid deformation due to moisture, rain, and sun, which will affect their use. ; When lifting, control the lifting speed, handle with care, and protect in place to avoid collisions.
(6) Emphasis on prior control, promptly provide operators with detailed explanations of construction technology, quality and finished product protection requirements before construction, foresee quality problems that are likely to occur during construction, and formulate some practical preventive measures in a targeted manner measure.
(7) Strengthen process control to ensure that there is an explanation before construction; there are inspections during construction, and quality problems such as weak supports, loose joints, uneven splicing, serious damage to the formwork, etc. must be rectified in place to control errors. Within the scope permitted by the specification; at the same time, we can make timely summaries after construction, learn lessons, and avoid similar quality problems from occurring again in the next construction. When setting up the mold, avoid impaction of the inner corners to prevent difficulty in removing the mold.
(8) When dismantling the formwork, a formwork disassembly plan should be prepared, the formwork disassembly time should be controlled, the operator should be given a detailed explanation, and the order of disassembly and disassembly should be clearly stated. It is strictly prohibited to pry and knock hard. The dismantled formwork should not fall freely, and should be handled with care and Clean up coding piles in a timely manner.
(9) Before each mold installation, clean the debris on the formwork, and then apply the isolation agent evenly without missing any paint to facilitate the disassembly of the formwork.
(10) In order to ensure the quality of the project, enhance the visual effect, and reduce the phenomenon of slurry leakage, honeycombing, and pitting during the concrete pouring process, when assembling the formwork, use double-sided tape to seal the seams and old bolt holes. , which can effectively reduce the occurrence of the above common quality problems.
(11) Supervisors should carefully review whether the template assembly plan is feasible and whether the safety measures are comprehensive. During the concealed acceptance, carefully check whether the requirements of the formulated plan have been implemented; carefully check the appearance of the formwork, support quality and support system, especially strengthen the strength of the formwork, seams, elevations, support systems, fasteners, etc. Inspect to ensure its forming quality and safety during construction.
3.Construction methods
3.1 For cast-in-place structures with a floor height not exceeding 5m, the columns, walls and beams can be cast in one go to reduce the joint deviation of the concrete of the main beams and wall panels caused by secondary formwork. At the same time, in order to prevent segregation of concrete during the pouring process, the height of a single pour should not be too high. When the height exceeds 3 meters, a chute should be added at a position of 2 meters.
3.2 Splicing of plywood formwork
When the plywood formwork is being spliced on a flat surface or at a corner, in order to ensure its airtight performance, the repeated tongue-and-groove and 45° bevel joint methods are used to connect, and the interface is reinforced with 48×100mm square wood.
3.3 Installation and fixation of plywood formwork
3.3.1 Column template
(1) Except for the 48×100mm square wood that repeats the tongue and groove on both sides of the column molding, the rest are fixed with ¢48 steel pipes as backing. This not only facilitates construction, but also effectively reduces the weight of the composite plate formwork. The spacing should not be greater than 150mm.
(2) The column formwork should be fixed with steel pipe hoops. The spacing is determined by the formwork design. Generally, the distance between the first pass and the floor is no more than 150mm. When the side length of the column section is 700~1000mm, a bolt with a diameter of 12 is used as a reinforcement in the middle. The open-web bolt in the column covers a plastic pipe with a diameter of 20, and customized plastic plugs are used at both ends to avoid the detrimental effects of cement slurry being poured into the pipe. take out. When the side length of the column section is 1000~1500mm, two 12-inch bolt fasteners are used in the middle.
(3) When the outer surface of the column is connected up and down, in order to prevent the joints from being dislocated up and down, reduce the grooving of the formwork and prevent the joints from not being vertical when reused, the column heads are reinforced with the bolts used when fixing the side formwork of the frame beam. Therefore, when setting the frame beam When fixing bolts on the outer formwork, consider the use of column and beam bolts.
3.3.2 Beam formwork
(1) The beam formwork adopts the method of wrapping the sides with the bottom, which facilitates the early removal of the side formwork without changing the section of the side formwork. When the beam width is not greater than 300mm, it is advisable to use 48mm thick hardwood 48 steel pipes for corrugation; when the beam width is greater than 300mm, it is advisable to use a split template combining plywood and 48×100mm wood corrugation, which will help increase the stiffness in the length direction.
(2) The beam side formwork should be made of plywood plus 40×50mm small wood corrugations. When the beam height is greater than 500mm, it should be reinforced with through-hole bolts with a diameter of not less than 10mm, using the same column reinforcement method.
(3) When columns and beams cross, the column formwork should be extended, and the beam formwork should be based on the column formwork to ensure the overall effect of the plane. At the same time, the beam side formwork should be configured according to the span and the modulus of the plywood into a formwork that can be assembled and easily disassembled to facilitate early disassembly and reuse of the beam side formwork.
(4) Determine the correct construction procedures. During the installation process, the bottom formwork of the beam should be supported and fixed first, and the formwork on both sides can be installed only after the beam steel bar binding is accepted and meets the requirements.
3.3.3 Wall formwork
(1) The wall formwork should use a combination formwork. Before assembly, pop up the wall edge control line according to the axis, and weld 16 steel bars 50mm from the floor of the bureau building as positioning control points. The steel bars at the welding points are cut with a grinding wheel cutting machine to avoid cutting sharp points with a steel bar cutting machine and embedding them in the plywood when tightening the wall tension bolts.
(2) During combined installation, the reserved openings should be pre-positioned according to size, and tightening bolts should be added around the reserved opening formwork to prevent displacement, deformation, bulging and slurry leakage at the external corners of the opening formwork during the vibration process. .
(3) The connection between the outer side of the wall formwork and the lower layer is fastened with the column root formwork. When making and installing the formwork and adding ribs, extend the ribs 250mm down so that the ribs coincide with the lower layer fastening bolts. To prevent slippage at the joint, stress deformation and mold running will occur, resulting in uneven joints between the upper and lower layers, resulting in staggered platforms.
3.3.4 Cast-in-place slab formwork
(1) The cast-in-place plate formwork is copied according to the bay size and plan. Combined with the module size of the plywood, a floor plan will be produced and processed separately. The semi-finished templates should be uniformly coated with isolation agent, marked with numbers and stacked in categories; the plywood seams in each layer and room should be arranged in the same manner, the direction when making changes should be consistent with the whole, and the wood grain and color of the material surface should be basically the same, so that the plywood seams should be consistent during installation and laying. Move the saw.
(2) The joints and fixation are connected and fixed with 48×100mm square wood. After the square wood is mechanically pressed and planed, it is then finely processed by hand and used in conjunction with 48 steel pipes.
(3) The support frame for the cast-in-place slab should be erected according to the design requirements. The top steel pipe should be erected in the short direction first, so that the steel pipes and square timber on site can be fully utilized. The spacing between steel pipes and square timbers should not be greater than 500mm, and the plywood must have sufficient resistance to twists and turns, and can bear the static and dynamic loads during concrete pouring.
(4) When dismantling the cast-in-place slab formwork, erect full-length scaffolding in strict accordance with the disassembly procedures to ensure the safety of formwork removal. It is strictly forbidden to knock hard on the edges and corners, and to prevent free falling to avoid damaging the edges and cracking the edge of the board. After dismantling, stack them according to categories, and remove the cement slurry before reusing.
During the construction process, if the above aspects can be achieved, common quality problems caused by formwork assembly problems can basically be avoided. It not only increases the number of formwork turnover times, reduces the project cost, but also improves the quality of the project and improves the look and feel of the concrete effective.